fig5
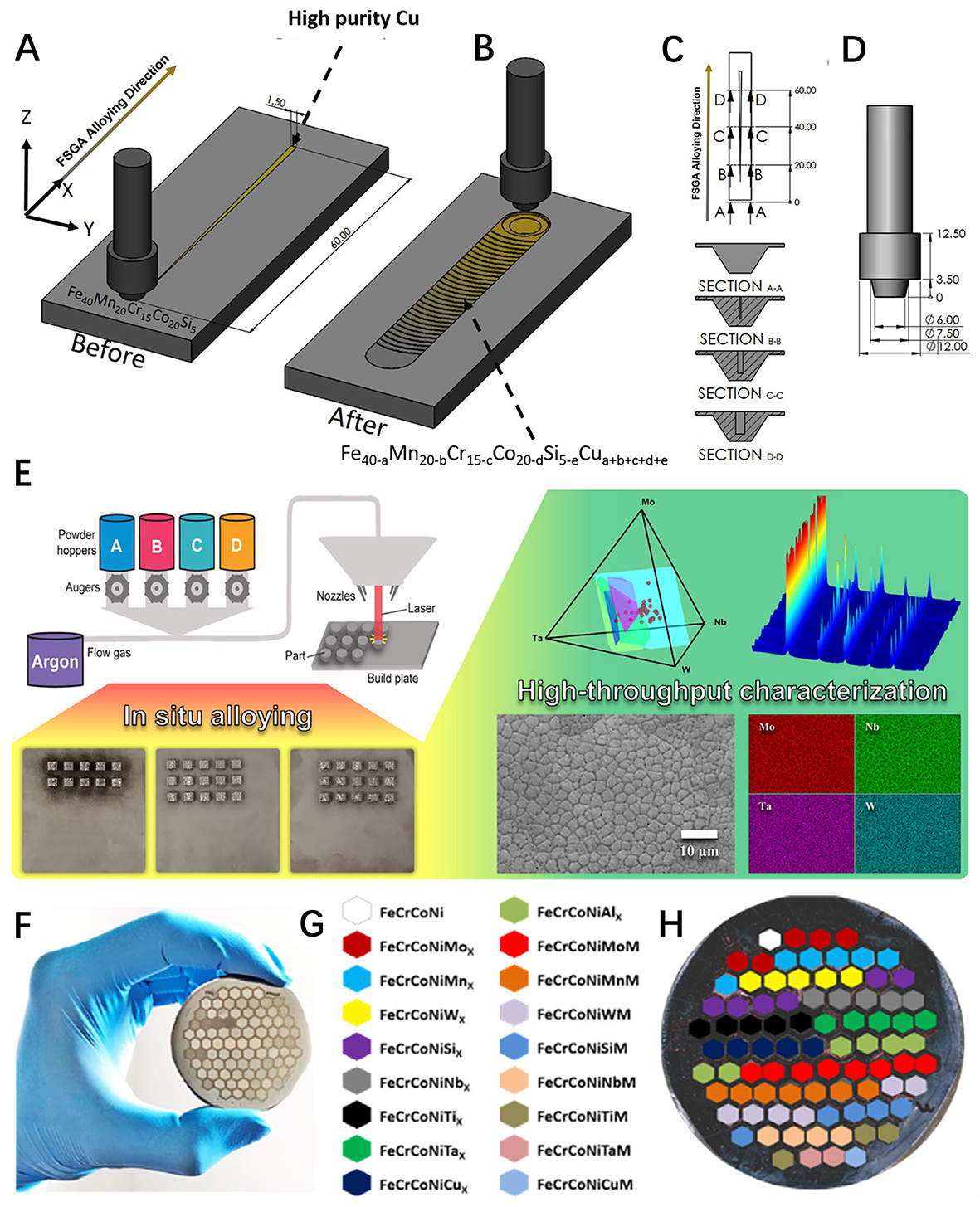
Figure 5. (A) Schematic of friction stir gradient alloying (FSGA) assembly showing tapered Cu section retrofitted in the groove created via CNC (Computer Numerical Control) milling on the base CS-HEA. The total length of the Cu section and groove is 60 mm, with at least 16 mm of base material on either side for tool plunging and retrieval (not drawn to scale). (B) Schematic of processed (alloyed) region after the FSGA process is completed. (C) Location of W-Re tool with respect to the tapered Cu plate during FSGA assembly and (D) design of the tool used in the current study. (E) Schematic of LENS MR-7 system, synthesized Mo-Nb-Ta-W arrays and corresponding HT characterization. (F, G) Design of honeycomb-structured HEAs. (A-D) Reproduced with permission[64]. Copyright 2020, Elsevier. (E) Reproduced with permission[67]. Copyright 2020, Elsevier. (F, G) Reproduced with permission[72]. Copyright 2020, Elsevier. HEA: high-entropy alloy.